Introduzione
Una buona pedalboard non è poi così difficile da costruire: l’ importante è conoscere i problemi a cui si andrà incontro e cercare di evitarli già nella fase di progettazione. Io normalmente le costruisco su due livelli, come quella in foto, affinché soddisfi due criteri importanti: solidità strutturale e pulizia nei cablaggi, il che si traduce in una sola parola: affidabilità. Inoltre i pedali, posizionati su due livelli, risultano più accessibili e comodi da raggiungere.
Odio vedere spinotti ballerini, cavi di segnale che passano accanto a cavi di alimentazione, ciabatte colme di alimentatori inutili, cablaggi fatti male. Un calcio mal dato ed ecco che non funzione più nulla, magari nel mezzo di un assolo. Andare a scovare il cavo o la presa maltrattata diventa un problema non indifferente, e così si termina la serata incavolati neri e con chitarra ed ampli in diretta (il che, a volte, non è affatto male).
E poi pedali che, fissati con il velcro (odio questo materiale), si staccano, si muovono e si impiastricciano di colla sul fondo…Ho preferito evitare questo materiale tanto in uso. Come ho preferito evitare alimentatori con uscite multiple, cavi multipli, cablaggi multipli: pesano molto, costano altrettanto ed offrono poco. Va da se che una pedaliera siffatta non è molto flessibile (peculiarità dei turnisti), ma è assemblata per coloro che già hanno precise idee in fatto di concatenazione degli effetti.
Una buona pedalboard è anche indice di un buon approccio del musicista verso gli strumenti musicali: l’ordine e la cura dei propri strumenti denota anche ordine e cura nel modo di suonare…Non è poca cosa.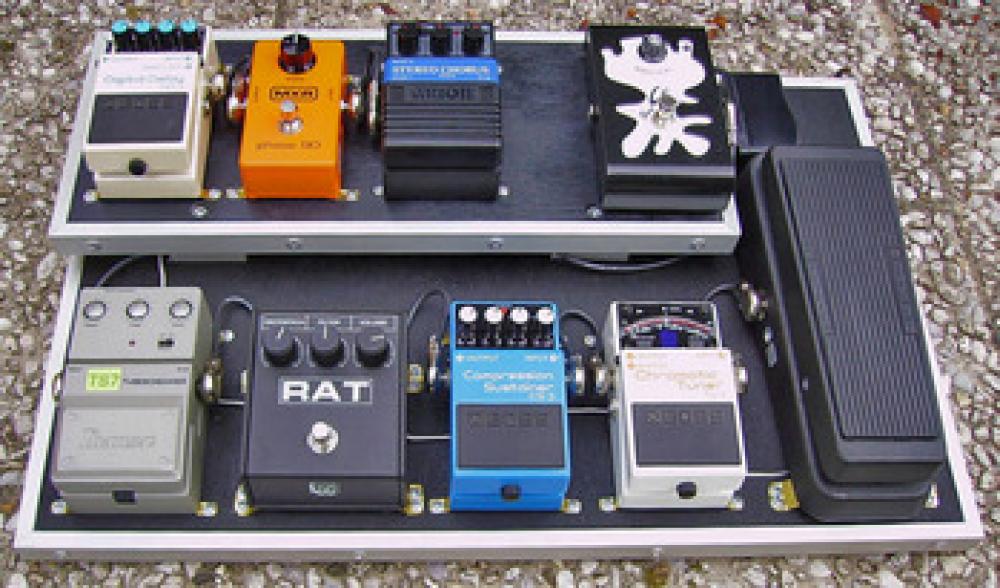
Venendo al sodo passo a descrivere step by step la costruzione della pedaliera visualizzata, costruita per un amico, conscio che qualcuno storcerà il naso per alcune scelte adottate e soluzioni inusuali: garantisco che sono scelte effettuate senza uso di allucinogeni od alcolici (limoncello in primis) bensì scelte ponderate dopo aver provato in prima persona attimi di panico ed arrabbiature varie. E dopo averne assemblate in quantità industriale seguendo sempre consigli e commenti dei musicisti amatori o professionisti.
Va da se che il progetto è semplice e si rivolge innanzi tutto alla fascia amatoriale. Ma non escludo di postare prossimamente progetti alquanto complessi destinati a professionisti, magari integrandoli con sistemi a Rack, True Bypass Switcher, Buffer, Midi System e chi più ne ha più ne metta...
Progettazione.
In questa fase viene definito il layout della pedaliera, compreso il posizionamento dell’alimentatore, la concatenazione dei pedali, la loro distanza ed il cablaggio in generale.Nel caso della pedaliera raffigurata il segnale entra nel Wah Wah, prosegue attraverso l’accordatore Boss TU2, compressore Boss CS3, Rat, Ibanez Tubescreamer TS7 per poi essere indirizzato verso l’input dell’ampli. Il tutto posizionato sulla base.
Sul livello superiore sono presenti 3 pedali di modulazione segnale: dal “send” dell’ampli arriva il segnale che entra in uno Stereo Chorus Arion, prosegue attraverso il Phase 90 MXR e il Delay DD3 Boss per poi rientrare nel “return” del loop effetti.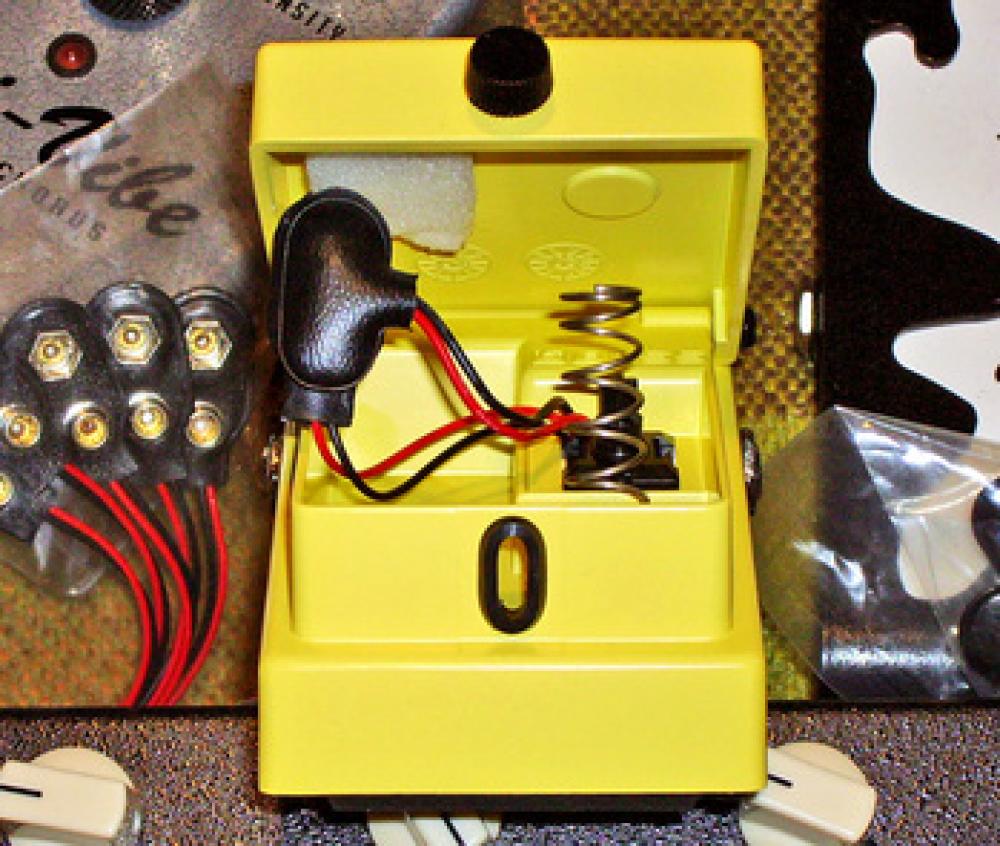
Un ulteriore spazio libero (rappresentato dal Boost Cat Drive della Advance) è previsto per un ulteriore upgrade del sistema. L’alimentatore switching è posizionato opportunamente sulla base nella zona anteriore al Wha. La pedaliera misura cm. 60 x 38 e quindi è relativamente poco ingombrante e facilmente trasportabile, nonché abbastanza leggera.
Posizionate i pedali su una tavola o foglio, tenete conto delle distanze per i vari spinotti e decidete le misure per voi idonee: a parte i pedali della EH, in una profondità di cm.38 ci possono stare la quasi totalità dei pedali in commercio. La lunghezza, logicamente, andrà stabilita in funzione della quantità di stomp box.
Un Wah tipo Cry Baby o Vox necessita di cm.14 di spazio per essere fissato come vedremo successivamente.
Costruzione struttura.
Materiale occorrente:
- N° 1 tavola di compensato da mm. 20 con dimensioni cm. 60 x 38 (Base).
- N° 1 tavola di compensato da mm. 20 con dimensioni cm. 46 x 19 (Sopralzo).
- N° 2 barre di profilato in alluminio a L (mm. 20 x 10) da mt. 2 di lunghezza.
- N° 1 barra di profilato in alluminio quadro (mm. 20 x 20) da mt. 2 di lunghezza.
- N° 2 tappi quadri in plastica (mm. 20 x 20) per la chiusura del profilato di cui sopra.
- N° 1 confezione di rivetti da mm. 4.8 x 16 di lunghezza.
- N° 1 rivettatrice.
- N° 4 piedini in gomma con relativi viti autofilettanti con diametro mm. 3.5 x 16.
- N° 5 viti ad esagono incassato (brugole) da mm. 6 x 50 con relativi dadi.
- N° 1 Spina da pannello tripolare a norme CEE 10A / 250 Volt.
- N° 2 prese da pannello da mm. 4 di diametro.
I componenti delle due ultime voci sono reperibili presso un qualsiasi rivenditore di elettronica mentre tutti gli altri componenti sono reperibili presso i negozi del “fai da te”, ferramenta e mercatoni vari.
La spesa totale non dovrebbe superare i 35 / 40 euro, rivettatrice compresa (che servirà anche per altri lavori casalinghi).
Come procedere alla costruzione della struttura:
- Tagliare il compensato nelle misure stabilite (servizio previsto nei centri fai da te). Tagliare le barre di profilato 20 x 10 che andranno successivamente fissate sui bordi della tavole di compensato. E’ consigliabile eseguire un taglio leggermente abbondate in lunghezza affinché possa essere meglio rifinito con una lima, in caso di mancanza di macchinario preciso. Gli angoli verranno smussati a 45°.
- Forare preventivamente i profilati a L (fori da mm. 5 di diametro) per il fissaggio con rivetti. I primi fori dovranno essere effettuati ad una distanza di almeno cm. 2.5 dai bordi.
- Fissare tramite morsetti o nastro da carrozziere i profilati alle tavole di compensato, forare e procedere con la rivettatura.
- A questo punto avremo le due tavole di compensato finite e pronte per essere unite tramite le 5 viti ad esagono incassato.
Fase successiva:
- Limare i bordi superiore ed inferiore della spina CEE da pannello portando lo spessore totale a mm. 20. (Si tratta di due bordini in plastica inopportuni).
- Tagliare il profilato quadro che andrà posizionato come in figura, con tappi di chiusura e spazio per presa CEE di alimentazione.
- Tagliare due spessori di angolare quadro che fungeranno da appoggio anteriore (cm. 6 / 8 di lunghezza)
- Fissare tutti gli elementi di profilato quadro in posizione utilizzando del nastro biadesivo.
- Completare l’assemblaggio semidefinitivo aggiungendo il sopralzo.
- Bloccare il tutto con qualche morsetto e forare con punta da mm. 6 di diametro. I fori devono essere completamente passanti, meglio se eseguiti su un trapano a colonna.
- A fori eseguiti smontare il tutto e riposarsi bevendo un caffè o una birra leggermente alcolica.
- Allargare i fori, sulla tavola superiore ed inferiore, per incassare la testa dei bulloni e delle viti: utilizzeremo lo stesso diametro di punta per testa e bulloni, che saranno incassati a pressione.
- Assemblare il tutto provvisoriamente verificando eventuali discrepanze. Praticare i 2 fori che servono per il montaggio della presa CEE. (mm. 2.5) e bloccare la stessa con due viti autofilettanti (mm.2.9).
A questo punto tagliare uno spezzone di profilato a L lungo una decina di centimetri: servirà per sostenere le due prese da pannello che nelle quali verrà inserito l’alimentatore switching (In questo caso da 800 milliampere, sufficiente all’alimentazione di tutta la pedalboard. Alimentatore che preventivamente avrete acquistato nello stesso negozio di componenti elettronici con un costo non superiore ai 20 / 25 euro).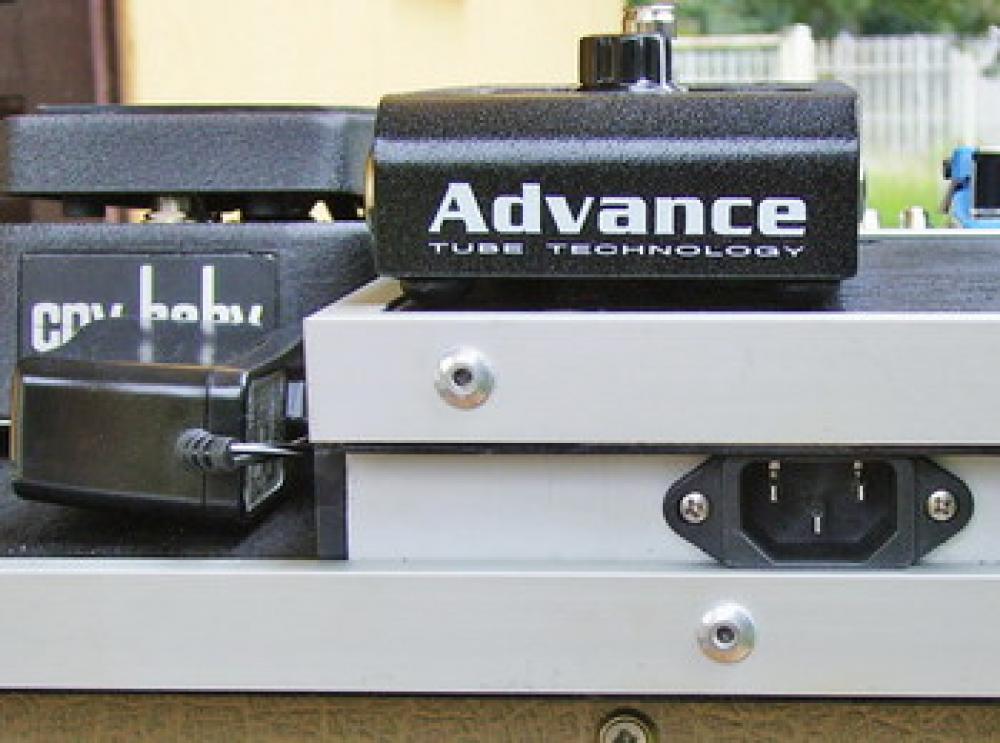
Bene, la struttura è pronta da verniciare: smontate il tutto, proteggete i profili in alluminio con nastro da carrozziere e verniciate con nero opaco acrilico o nitro in bomboletta. Il giorno seguente potrete proseguire con il cablaggio.
Un alimentatore da 800 milliampere può alimentare 50 e più pedali overdrive o distorsori, che assorbono circa 15 milliampere cadauno. Pedali Chorus e di modulazione possono assorbire 50 milliampere cadauno mentre pedali digitali possono assorbire un centinaio di milliampere cadauno. Leggetevi le caratteristiche dei vostri pedali ed utilizzate un alimentatore idoneo e non esagerato, tenendo anche presente che i pedali non saranno mai contemporaneamente accesi. Un alimentatore switching da 1.7 Ampere è simile come dimensioni al nostro da 800 milliampere e può alimentare una quantità enorme di pedali.
Specificate al negoziante che avete necessità di un buon alimentatore stabilizzato switching a basso ripple. Costano pochi euro in più ma vi garantiscono assenza di rumori di fondo.
Alimentazione pedaliera.
L’alimentazione avviene attraverso la spina da pannello CEE (e naturalmente attraverso un cavo con presa CEE adeguata che troverete nello stesso negozio di elettronica a pochi euro). Un cavo bipolare saldato alla stessa alimenta a sua volta la due prese a pannello posizionate sul profilato ad L appena tagliato. Questo ultimo angolare verrà posizionato al limite destro del piano superiore. L’alimentatore andrà posizionato come da foto. Le saldature andranno protette da guaina termorestringente o nastro isolante, per maggior sicurezza e protezione.
Alimentazione pedali.
Odio gli spinotti mobili, di tutti i tipi, soprattutto quelli che sono a saldare. Non sono affidabili, sono sempre a rischio pedate e, per la maggior parte delle volte sono causa di guai, cortocircuiti ed interruzioni repentine di tutto il sistema. Io non li uso più.
Come fare allora? La risposta è molto semplice, soprattutto se i pedali vengono alimentati da batteria a 9 Volt. Si acquistano delle clips per batteria (che sono già dotate di cavetto rosso / nero) e si alimentano i pedali tramite queste.
Praticamente si deve analizzare pedale per pedale: alcuni hanno uno sportellino inferiore attraverso il quale far uscire il cavetto mentre altri hanno il fondo asportabile tramite viti. In questo ultimo caso è sufficiente praticare sul fondo un forellino da mm. 2 di diametro da cui fare uscire il cavetto. Il valore del pedale non ne risentirà, mentre l’affidabilità sarà massima. Nei pedali tipo Boss lo stesso cavetto passerà attraverso le fenditure esistenti per poi raggiungere facilmente il fondo. A questo punto il cavo rosso diventerà il negativo mentre il cavo nero il positivo (si invertono i colori della polarità). Non resta che unire in parallelo tutti i cavi rossi e tutti i cavi neri, farli passare al di sotto dei pedali ed arrivare all’alimentatore. Più semplice e pulito di così non esiste…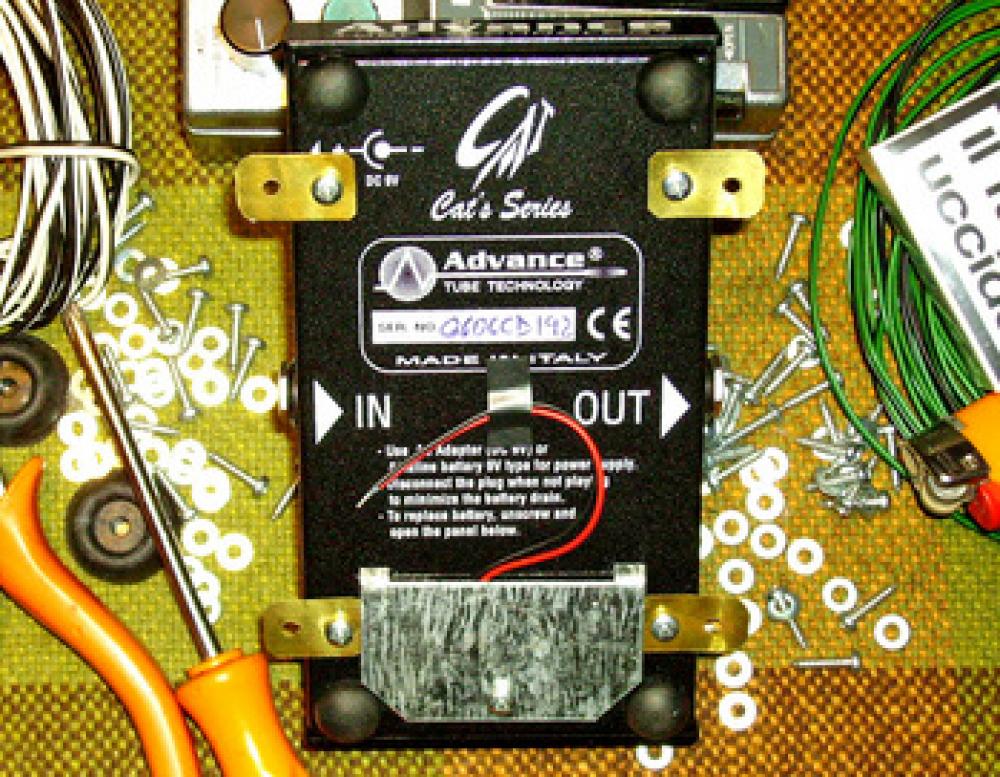
Nelle foto si vedono dei cavi bianco / nero intercorrere tra un pedale all’altro: non sono altro che cavi di prolunga saldati a quelli delle clips, nastrati e posizionati sotto il pedale stesso. I cavetti di alimentazione dei pedali posti sul piano superiore passeranno attraverso un foro posizionato sulla tavola al di sotto dei pedali stessi, per poi venire collegati in parallelo anch’essi.
Pulizia, ordine e affidabilità.
Cavi di segnale.
Naturalmente autocostruiti. Io uso cavi George L’s .155 (quelli più sottili) mentre per gli spinotti uso quelli commerciali a pipa saldati al cavo. Una buona saldatura, con questi tipi di spinotti, si esegue carteggiando un poco la superficie di contatto e quindi preriscaldandola non troppo con saldatore da 50 Watt ed un ottimo stagno SN/PB 60 / 40. Il costo di un metro di cavo si aggira attorno a 3.5 euro mentre gli spinotti costano circa 50 cents cadauno. Un tester anche economico è consigliato per controllare la funzionalità del cavo con gli spinotti saldati. Non uso i jack angolari George L’s: sono avvitati, col tempo possono creare problemi, costano eccessivamente e sono pure ingombranti.
Come fissare i pedali.
Come già detto odio il velcro per molti motivi: i pedali sono ballerini, a volte si staccano, il velcro si impatacca al pedale…. Non buono, a mio parere. Assolutamente inaffidabile. Io mi sono comprato una striscia di ottone da due decimi di millimetro di spessore e la uso per fissarci di tutto. Con viti.
L’ottone si taglia con una forbice a strisce da un centimetro circa, lo si ritaglia successivamente alla lunghezza desiderata e lo si fora con punta da 3 millimetri. In un foro si inserisce la vite che blocca il fondo del pedalino mentre nell’altro foro si inserisce una vite autofilettante con rondella nella tavola di compensato. I pedali non si muoveranno e non si staccheranno nemmeno con uso intensivo. Per il Wah ed altri pedali “importanti” si possono tagliare strisce più larghe e fissare il tutto con 2 viti. Se non trovate l’ottone vanno bene anche i lamierini di un vecchio cartello dei gelati (quelli esposti davanti ai bar). Fatevene regalare uno che per 2567 pedaliere ne avrete a sufficienza.
Ma l’ottone è più professionale, costa veramente poco e non arrugginisce…
Verifica finale.
I pedali si accendono tutti? Il segnale raggiunge l’ampli? In caso non si accendesse nessun pedale probabilmente avrete invertito qualche polarità. Ricontrollate pedale per pedale con un tester.
Il segnale non arriva all’ampli? Controllate prima i cavi esterni e se il volume chitarra / ampli sia in posizione adeguata…prima di maledire l’autore di questo articolo. Nel caso che i cavi ed i volumi siano a posto controllate con il solito tester i cavetti che avete saldato precedentemente. Nel caso di cavetto difettoso maledite voi stessi: io non c’entro per nulla!
Eseguite con calma tutte le operazioni e soprattutto non abbiate fretta. Solo così avrete alla fine un lavoro ben fatto che vi accompagnerà per molto tempo…Cioè fino al prossimo cambio di pedali...
Gia pronta e funzionante? Siete più veloci di un lampo e comunque più veloci del sottoscritto nel redigere questo articolo.
Ora non vi resta che farvi costruire un case ad hoc, un borsone in finta pelle imbottito oppure cercare un trolley od una valigia rigida in cui riporre il tutto. Ultima cosa: non dimenticatevi di suonare. A volte il fai da te è più libidinoso dello studio della chitarra...
Ciao.
Lauro.
Alecb.
Foto posizionamento alimentatore
Foto posizionamento pedali
Foto della base
Foto materiale da ferramenta
Foto materiale elettrico